
Adjustable-Length Transfer Board for Mechanical Wheelchair Users
A Pitt Bioengineering Senior Design Project

Unmet Clinical Need
Our project inspiration stemmed from my groupmate's co-op experience at the Human Engineering Research Lab (HERL). He brought us to bi-weekly Spinal Cord Injury (SCI) Support Group meetings held by UPMC Mercy, where we interacted with patients and found that many use transfer boards to move from their chair to other locations like their bed, car, etc. These boards can be used independently, but lack safety and stability. We first aimed to redesign standard boards to improve these qualities.

After bringing our minimum viable product (MVP) to the SCI meeting, the feedback we received was that the main issue with transfer boards was not being addressed by our idea. Many manual wheelchair users (MWUs) carry multiple boards of different lengths that they need for different transfer scenarios throughout the day.

We altered our design plan with the help of the machine shop to create a schematic for an adjustable length frame of 80/20 aluminum T-slots.

This prototype mimics the intended functionality of our final model, however it does not contain a latch for anchoring the board length or have the necessary structural integrity. Our next prototype aims to implement the intended materials for a final design that will undergo verification and validation testing.

After bringing our minimum viable product (MVP) to the SCI meeting, the feedback we received was that the main issue with transfer boards was not being addressed by our idea. Many manual wheelchair users (MWUs) carry multiple boards of different lengths that they need for different transfer scenarios throughout the day.

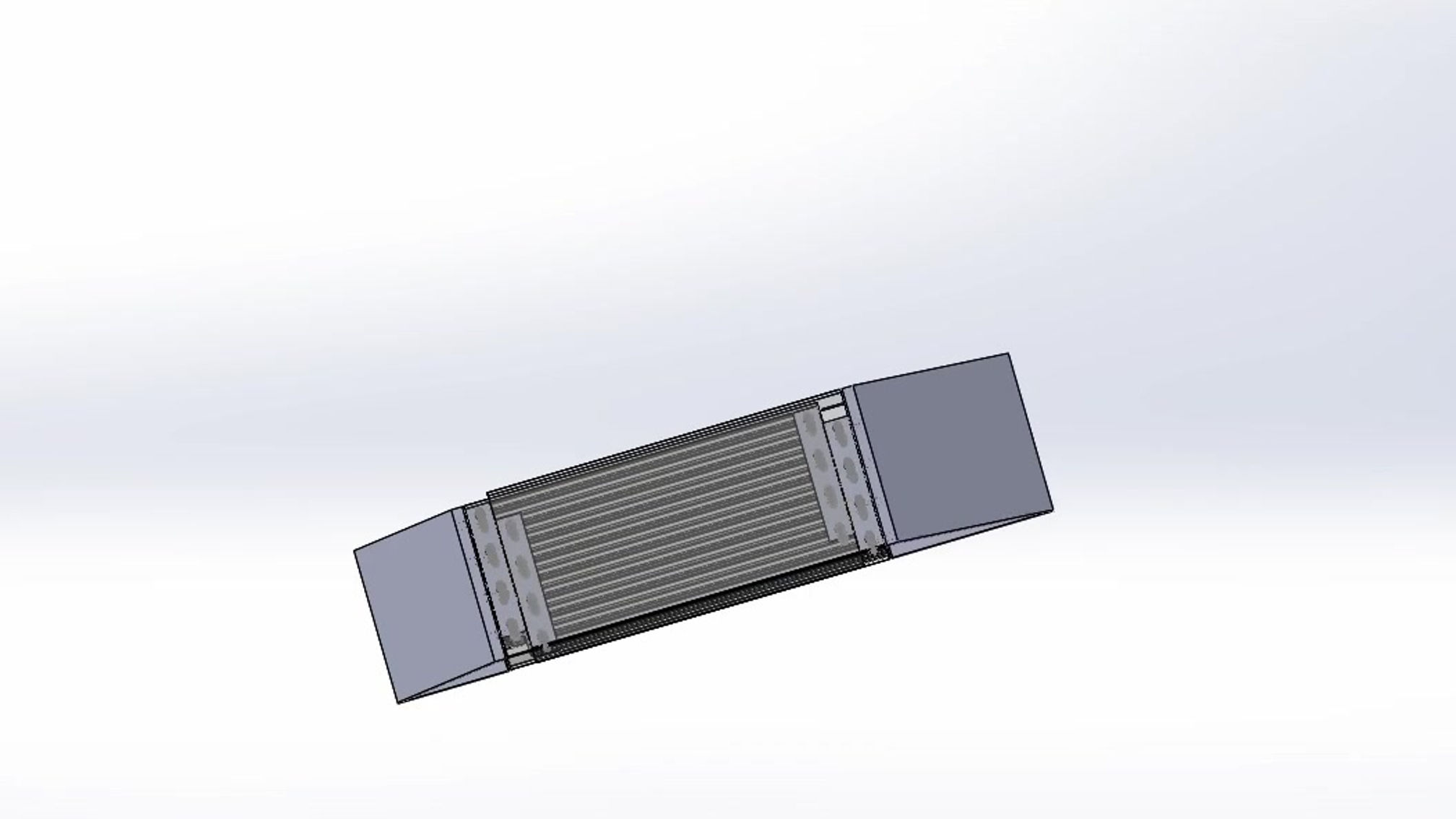


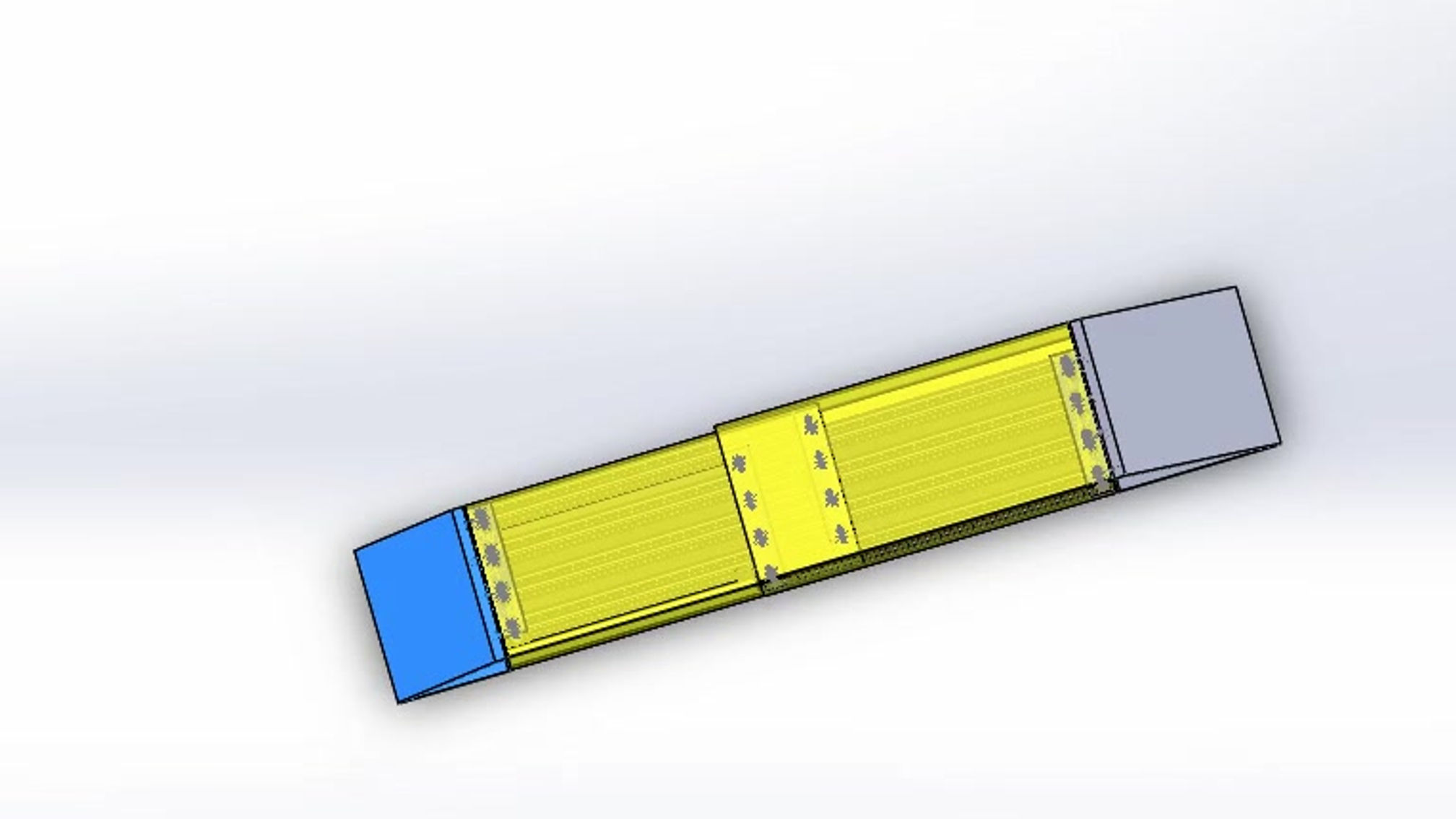
Project Contribution
As team lead, my role on this project team consisted of a majority of the design and physical fabrication, as well as team management and documentation. From our minimum viable prototype (MVP) to our final physical model (not completed) I worked closely with Jeff Speakman in the Swanson Center for Product Innovation throughout the entire design process. This included assessing design specifications for part selection, material testing, laser cutting, acrylic welding, developing a method to cut and bend the covers, fine tuning our SolidWorks model, and contributing to assembly of the final design. I also contributed to a large portion of the documentation throughout the year, specifically taking ownership of developing a new Weight Bearing Verification Test Protocol and Test Report using finite element analysis (FEA) to evaluate the strength of our device once a physical model was inaccessible. I also created the motion study clips included in a video we created to conduct remote validation testing via survey. Ultimately, I learned a great deal about the design process, SolidWorks, physical fabrication methods, design controls, proper documentation, and leading a team.
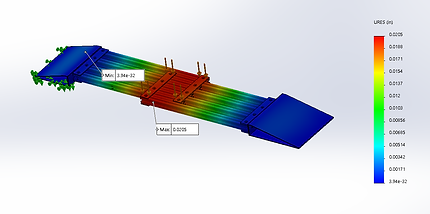